It would be really hard to go through a typical day in the developed world without running across something made from ABS plastic. It’s literally all over the place, from toothbrush handles to refrigerator interiors to car dashboards to computer keyboards. Many houses are plumbed with pipes extruded from ABS, and it lives in rolls next to millions of 3D-printers, loved and hated by those who use and misuse it. And in the form of LEGO bricks, it lurks on carpets in the dark rooms of children around the world, ready to puncture the bare feet of their parents.
ABS is so ubiquitous that it makes sense to take a look at this material in terms of its chemistry and its properties. As we’ll see, ABS isn’t just a single plastic, but a mixture that takes the best properties of its components to create one of the most versatile plastics in the world.
All for One
Unlike simple plastics such as polylactic acid (PLA), which we discussed earlier, ABS, or acrylonitrile butadiene styrene, is a copolymer. That means that instead of linking together a single type of monomer into long chains, multiple different monomers are linked together. In the case of ABS, it’s three monomers, and they’re all right there in the name — acrylonitrile, butadiene, and styrene.
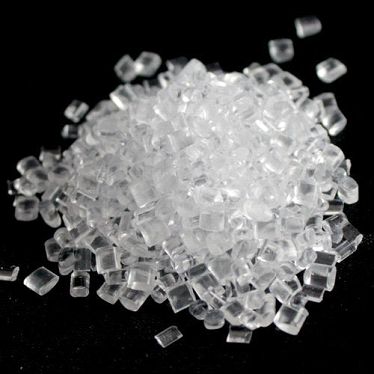
How these three components got together is an interesting story. Back as far as the 1930s, chemists in the still-infant polymer industry were experimenting with both polyacrylonitrile (PAN) and polystyrene (PS). PAN was an early success in the search for synthetic fibers, resulting in such products as Orlon acrylic. The synthetic fibers, as well as other copolymers of PAN, found their way into everything from clothing to carpets. Polystyrene was also commercialized around the same time, initially as a replacement for zinc in the die-casting of small parts. The clear plastic was hard, but brittle and with a low melting point.
By the 1940s, polymer chemists had figured out that copolymerizing styrene and acrylonitrile monomers would result in a plastic that was still clear like polystyrene, but less brittle and with better thermal properties. The plastic was called styrene-acrylonitrile (SAN) and found use in the food packing industry, and for making a variety of consumer products.
While SAN was better than pure polystyrene for many applications, it still lacked enough toughness to be used for some applications. So in the late 1940s, chemists decided to add another polymer to the mix: polybutadiene. Polybutadiene, or synthetic rubber, had been around since 1910 and has many of the properties of natural rubber — flexibility, ductility, wear resistance — leading to its use in everything from motor vehicle tires, to seals and gaskets, to golf balls.
Add a Little Rubber
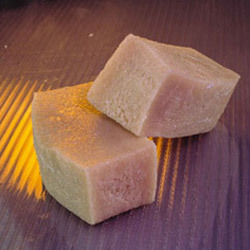
Butadiene seemed like a natural addition to the polymer soup of SAN, and in 1948, ABS was invented. With the strength of acrylic, the hardness of styrene, and the toughness of butadiene, the copolymer had a lot of new applications waiting for it. This was mainly due to the ability to control its properties by changing the mix of the three components. The plastic can be optimized for the application, and for the manufacturing method — tweak it a little and you’ve got a plastic with great properties for extrusion, allowing such products as ABS pipes and 3D-printer filament. Change the mix and the plastic works better for injection molding, resulting in myriad parts small and large, including, of course, LEGO.
It would be a mistake to think that ABS is simply three plastics melted together, though. ABS manufacture is a complicated process that has changed markedly over the years. Initially, an emulsion process was favored, where butadiene was first batch polymerized in an aqueous solution; acrylonitrile and styrene monomers were then added to the synthetic latex soup and allowed to polymerize. Little particles of ABS would form in the liquid, which could be extracted through centrifugation.

The mass polymerization method is favored now. In it, polybutadiene is produced separately, chopped into tiny fragments, and mixed with the acrylonitrile and styrene monomers. The batch is vigorously mixed during polymerization, which shears the polybutadiene chunks into even smaller sizes. The degree of mixing controls the size of the rubber particles and therefore the toughness of the plastic. It also controls the glossiness of the finished plastic, which is always very glossy when produced by the emulsion method since the liquid latex emulsion results in very small butadiene particles.
New ABS for Old
The market for ABS is huge. About 10.8 million tons of ABS resin were produced in 2016, and demand increases as new consumer products take advantage of the wide range of properties that can be dialed into the resin by changing the recipe slightly. Production of ABS is resource intensive, though. All of the monomers are derived at least in part from petroleum, and takes a lot of energy to create. Luckily, ABS is very recyclable, with used plastic being shredded and mixed to virgin ABS to form new pellets of almost the same quality of new plastic.
[Featured images credit: Alan Chia [CC BY-SA 2.0], via Wikimedia Commons]